Types of Positive Protection Barriers
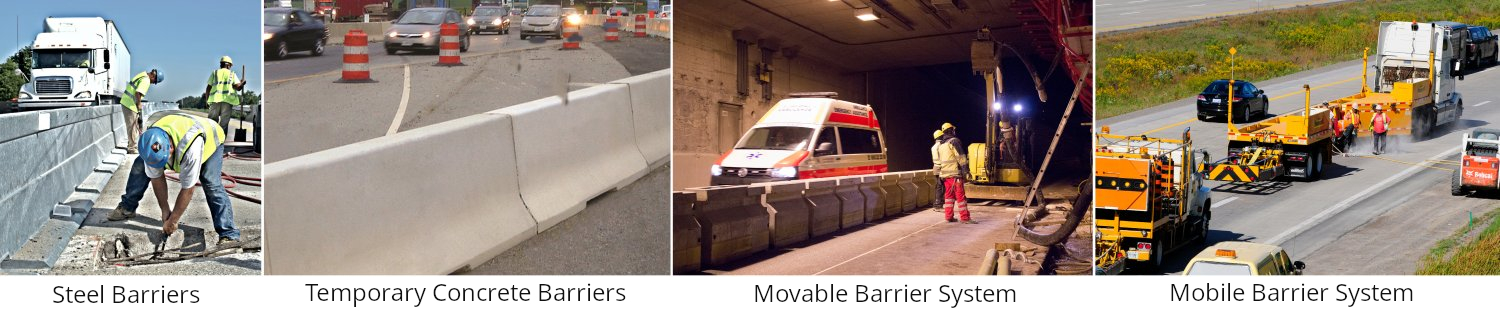
Protecting People from Preventable Injury and Death
Highway barriers or traffic barriers are a fundamental component of modern work zone design and traffic control engineering. The USDOT Safe System Approach and FHWA Safe System Roadway Design Hierarchy (based on the "Hierarchy of Controls" workplace safety protocol) emphasize that death/serious injury is unacceptable and safety is proactive (e.g. engineering in and using Positive Protection barriers proactively to seperate workers from traffic).
Road construction and maintenance projects often have serious hazards to be managed (with high-speed traffic moving within feet of pedestrian workers, roadside hazards, and/or little or no means for pedestrian workers to escape from errant vehicles). In a 2025 national survey, 60% of highway contractors reported crashes into their work zones. [6] A December 2024 IIHS study found that modern taller SUVs and pickups put pedestrians at very high risk (i.e. a highway worker has a 85% likelihood of severe injury when struck at 33 mph and an 85% likelihood of dying when struck at 45 mph by a median U.S. pickup). [18]
Fortunately, Positive Protection barriers can be used to directly control these hazards to highway workers, who are among the most "Vulnerable Road Users". Federal law (23 CFR 630.1108(a)) and ANSI standards (A10.47-2021 §4.4) specify types of projects (e.g. tunnels, bridges, drop-offs, etc.) which require Positive Protection & barrier separation. For such projects, a “separate pay item” for Positive Protection is required under federal law and regulations.
Positive Protection are devices placed "between workers and motorized traffic" which function to "contain and/or redirect vehicles" and which meet applicable crashworthiness criteria (see 23 U.S.C. § 112(g) and 23 C.F.R. § 630.1104).
MASH certified traffic barriers placed between workers and motorized traffic (i.e. Positive Protection) offer state-of-the-art safety for workers and motorists by physically preventing (i.e. containing and/or redirecting) high-speed motorized vehicles from colliding with workers and other dangerous obstacles inside a work zone. A physical barrier (i.e. Positive Protection) provides one of the best possible protection solutions for workers exposed to the flow of traffic and is a common-sense and cost-effective way to prevent death and injuries of workers on roads and highways. In a national survey, 89% of highway contractors think Positive Protection barriers would help improve safety and prevent these horrific crashes. [4]
Historically, Temporary Concrete Barrier (e.g. K-rail or Jersey Barrier) was one of the only types of Positive Protection barrier available. With a weight of more than 4,000 lbs, Temporary Concrete Barrier requires heavy equipment to install, rearrange, and remove. As a result, Temporary Concrete Barrier often must be left-in-place for the duration of a project, limiting roadway capacity and flexibility to respond to rush hour traffic congestion.
Modern types of Positive Protection barrier such as Mobile Barriers, Movable Barriers, and Temporary Steel Barriers have made it practical and cost-effective for engineers and contractors to deploy Positive Protection on a wide range of projects (including short-term and short-duration projects). Mobile Barriers, Movable Barriers, and Temporary Steel Barriers offer more flexibility in work zone design and enable engineers and contractors to prevent work zone intrusions while also accelerating highway construction/maintenance projects and increasing roadway capacity to match daily traffic patterns.
What are the Types of Positive Protection?
Mobile Barriers
Mobile Barriers MBT-1® is a innovative traffic barrier system for work zones & incident response. The mobility of the MBT-1® allows rapid work zone setup/removal and enables engineers and managers to reduce project duration & cost, schedule around peak traffic hours, and minimize roadway congestion. The MBT-1® provides positive protection for a wide range of projects including short-duration and short-term work zones, road & bridge construction & maintenance, moving operations, incident management, and more. The MBT-1® has been called the "perfect tool" for various types of road, bridge, and tunnel projects.
The MBT-1® provides 42-102 feet of positive protection with minimal deflection and is tested and accepted under NCHRP 350 & MASH for TL-2 and TL-3 usage. Beyond its protective capabilities, the workhorse MBT-1® offers 85,000 lbs (38500 kg) GVWR carry capacity, optional crane & heavy lifting capabilities, generator power, high-lumen work lights for night operations, signage (e.g. matrix or arrow board), truck mounted attenuator (TMA), lockable storage, and more for enhanced safety and productivity on-site.
Moveable Barrier - Concrete
Lindsay Transportation Solutions QMB Zipper: The Road Zipper System is designed to increase capacity and reduce congestion by making more efficient use of new or existing roadways & highways. This innovative highway barrier is used for managed lanes and construction applications to create safe, dynamic highways that offer real-time roadway reconfiguration while maintaining positive barrier protection between lanes. The Road Zipper System can be used to move barrier from one side of a lane to the other to create work space and reopen lanes again to restore capacity.
Moveable Barrier - Steel
Valtir's Vulcan® moveable steel barrier is comprised of lightweight, galvanized steel segments that offers real-time roadway reconfiguration. This highway barrier is tested to NCHRP Report 350 Test Level 3 and Test Level 4, and EN1317 H2 and N2 specifications. The Vulcan® Moveable Barrier is designed for easier movement with the Vulcan® Transfer Attachment (VTA) when connected to a skid steer or front end loader. The VTA is also designed to help the operator work from either side of the barrier.
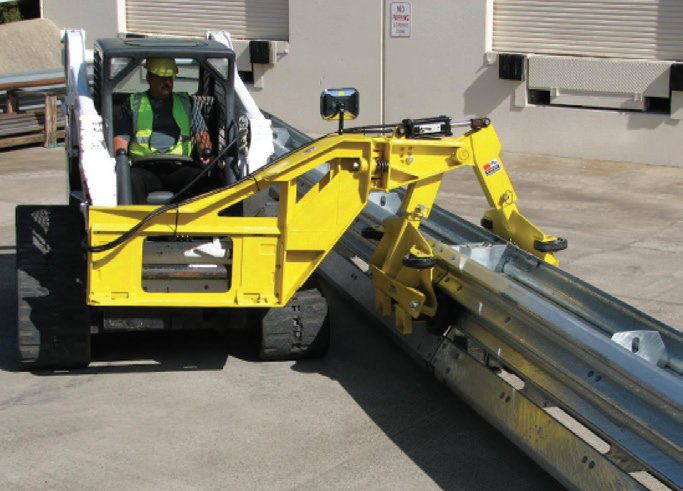
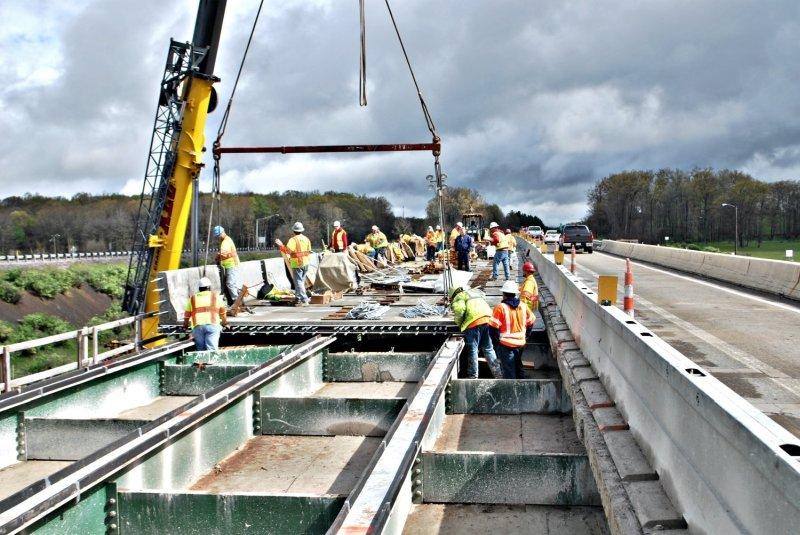
Temporary Steel Barrier
Hill & Smith Zoneguard® temporary steel barrier, offers the road construction industry an innovative temporary highway barrier solution that provides superior protection. A cost-effective alternative to traditional concrete barrier, Zoneguard’s lightweight configuration allows 750 feet to be hauled on one truck and up to 1500 feet to be installed in one hour. Zoneguard’s low weight does not affect its performance, as it meets both NCHRP 350 (TL-3 & TL-4) and MASH (TL-3) crash test standards.
Traditional Temporary Concrete Barrier (TCB)
Traditional temporary concrete barrier (TCB) is generally considered a device for use on Long-Term Projects. With a weight of 4,000 lbs or more, concrete temporary barrier (TCB) requires heavy equipment to install, rearrange, and remove at the end of a project. Temporary concrete barrier (TCB) often requires minimum deployment lengths, anchoring, and/or buffer area to be engineered into work zone plans.
As a result, temporary concrete barrier (TCB) is often left-in-place for the duration of a project, limiting roadway capacity & flexibility to respond to rush hour traffic congestion. Commonly cited challenges of using temporary concrete barrier (TCB) include installation/removal time & cost, safety risks of installation/removal in live traffic, and impracticality for Short-Term and Short-Duration work zones and/or where it is desirable to reopen lanes and relieve congestion for rush hour highway traffic.
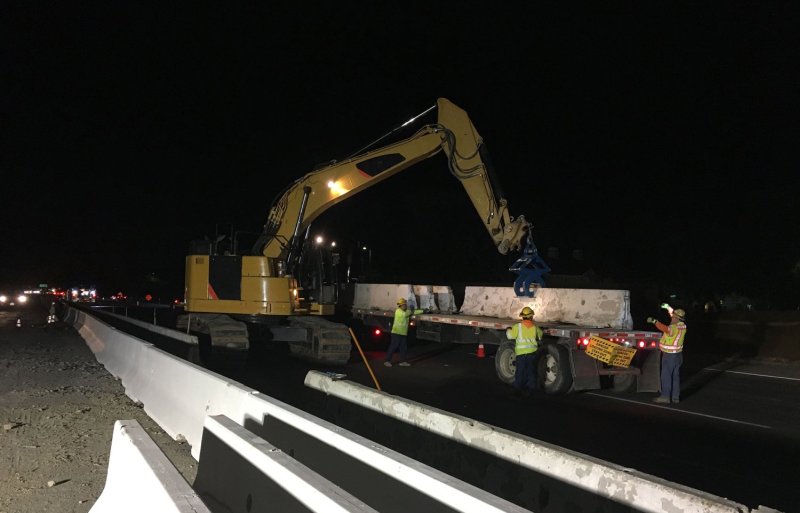
Unanchored/free-standing temporary concrete barrier (TCB) has greater lateral deflection. Unanchored TCB requires additional buffer/clear area which may reduce roadway capacity.
Anchoring temporary concrete barrier (TCB) reduces deflection. However, anchoring TCB increases installation/removal time & cost.
Why Proactively use Positive Protection?
"...safety, health, and well-being are inherent rights of every worker."
Today, we have the technology, 'know how', and responsiblity to protect workers from errant vehicles by using Positive Protection barriers. A physical barrier provides one of the best possible protection solutions for workers exposed to the flow of traffic and is a common-sense and cost-effective way to prevent death and injuries of workers on roads and highways.
"Definition: A positive protective device is a barrier that, when contacted by a motorized vehicle, is designed to redirect traffic away from the area it is set up to protect. A positive protective device may be made of steel, concrete, or any other material that will substantially protect workers and equipment from vehicle intrusions into the workspace. Positive protection devices provide separation between workers and motorists and can help improve traffic flows and mobility. "
In a 2025 national survey, 60% of highway contractors reported crashes into their work zones. [6] FHWA, USDOT, 2011 AAA, and 2024 IIHS studies confirm that motorized traffic poses a serious hazard to people working on or along our roadways:
- When struck by a vehicle at 30 MPH (44 feet/second), 40-53% of pedestrians (i.e. workers on foot) would likely be severely injured or killed. [15] [16] [17] [18]
- When struck by a vehicle at 40 MPH (59 feet/second), 75-85% of pedestrians (i.e. workers on foot) would likely be severely injured or killed. [15] [16] [17] [18]
- When struck by a vehicle at 50 MPH (73 feet/second), 90-100% of pedestrians (i.e. workers on foot) would likely be severely injured or killed. [16] [17] [18]
“As crash speed increases from 15 mph to 35 mph, the risk of a serious injury [for a pedestrian] goes from 9% to 52% when a median-height car is involved. With a median pickup, the risk [of a serious injury for a pedestrian] shoots up from 11% to 91% [as crash speed increases from 15 mph to 35 mph]... The findings point to the need for policymakers and traffic engineers to account for the makeup of the U.S. fleet. A commonly used benchmark for a 'safe' crash speed is one at which the risk of serious injury is 10% or less.”
The USDOT Safe System Approach emphasizes that death/serious injury is unacceptable and that safety is proactive (e.g. proactively engineering in and using Positive Protection barriers). In 2024, FHWA introduced the "Safe System Roadway Design Hierarchy" which is "emulated from the hierarchy of controls" workplace safety protocol. It prioritizes controls that "Remove Severe Conflicts" which includes solutions that provide "physical separation between motorized and non-motorized users" (e.g. Positive Protection barriers physically seperate highway workers from motorized vehicles).
"Focus on the hierarchy of controls (risk treatments) to design a workplace where pedestrian employees do not encounter moving vehicles, materials and similar hazards."
Professional workplace safety protocols such as the "Safety Hierarchy", "Hierarchy of Controls" , and "High-energy control assessment (HECA)" prioritize hazard elimination followed by implementing direct controls (e.g. Positive Protection barriers) to address high-energy hazards (e.g. errant moving vehicles). "Direct controls are actions that...reduce or eliminate the energy associated with these high-energy hazards... A barrier alongside a busy highway is a direct control for the kinetic energy of motor vehicles." [7]
- Most Effective:
- Physical barriers are considered one of the best possible protection solutions for workers exposed to the flow of traffic.
- Less Effective:
- Speed limits and speed enforcement. They are considered less effective at ensuring highway worker safety because they rely on road users for protective effect.
- Least Effective:
- Alarms, alerts, and channelizing cones/barrels. They are considered least effective at ensuring highway worker safety because they rely on road users for protective effect.
"[H]ow can we apply the concept of the hierarchy of controls to reduce the risk of work zone intrusions? 1. Avoid single lane closures... 2.Use barriers, not barrels. If traffic must pass by the work zone, employers should attempt to isolate workers from motorists as much as possible. The best way to do this in highway work zones is to use positive protection... Cones and barrels provide little or no protection from intrusions... 3. Control the speed of traffic... 4. Raising awareness... "

In an April 2021 CPWR webinar, a highway contractor reflected on a work zone intrusion on Highway 94 in California: In a posted 45 MPH work zone, a drowsey driver fell asleep and drifted right into a lane closure at 70 MPH striking multiple cones. The vehicle continued unimpeded for 3 seconds, when it struck a 41-year old employee (who was a husband, father and son) and threw him more than 50 feet. He died at the scene. In June 2021, the contractor joined in efforts calling on industry and roadway owners "to update state standard specifications to give stronger consideration to the use of barriers between workers and motorists."
"Cones and barrels are not positive protection. They are easy to deploy and easy for motorists to see, but aren’t effective at stopping or redirecting vehicles that intrude into the work zone. Shifting away from cones and barrels to the widespread use of positive protection may be the single most important step we can take to protect [lives]... in highway work zones."
Federal law (23 CFR 630.1108(a)) and ANSI standards (A10.47-2021 §4.4) direct that positive protection “shall be used” in, at minimum, 5 circumstances. For such projects, a “separate pay item” for Positive Protection is required under federal law and regulations. In 2021, the Infrastructure Investment and Jobs Act (IIJA) amended the Highway Safety Improvement Program (HSIP) to add protection for "Vulnerable Road Users", which includes road construction & highway workers on foot in work zones.
"Creating a protective barrier between motorists and workers is an essential step. This enables workers to perform their tasks safely while motorists move about the roadway. Based on the established traffic control plan, decision-makers must determine which barriers will best protect motorists and workers.
[ANSI Standard] A10.47[-2021 (§4.4)] states that positive protection measures need to be considered for each of these working conditions:
- Working zones that provide no means of escape (e.g., tunnels, bridges) from external motorized traffic intruding into the workspace
- Long duration work zones (e.g., two weeks or more) resulting in substantial employee exposure to motorized traffic
- Projects with high anticipated operating speeds (e.g., at least 45 mph or 72 km/h), especially when combined with high traffic volumes (more than 20,000 vehicles per day)
- Work operations that place employees within one-lane-width of travel lanes open to traffic
- Roadside hazards, such as drop-offs or unfinished bridge decks, that will remain in place overnight or longer"
Federal Highway Administration (FHWA) requires all new road safety hardware utilized on a federal aid eligible roadway to be tested using testing criteria reported in MASH. [14] MASH certified traffic barriers (i.e. Positive Protection) offer state-of-the-art safety for workers and motorists and physically prevent motorized vehicles from colliding with workers and other dangerous obstacles inside a work zone.
"Roadway work zones are some of the busiest, and potentially most hazardous, work environments you can find, as workers perform tasks in close proximity to vehicles that are often traveling at high speeds."
"MASH compliance could be the difference between life and death during a high-speed crash which is why it is crucial for every road system."
Without speed-appropriate barriers between live traffic and work zones (i.e. Positive Protection), both drivers & roadside workers face increased risk of serious injury or death from errant drivers. The benefits of complying with MASH include:
- State-of-the-art safety measures for workers
- Helping save the lives of drivers & passengers
"Motorists will inevitably make mistakes. Too often they pay for their mistakes with their lives – or the lives of innocent bystanders.... We have the technology and 'know how' to build our roadway system to anticipate user error. It can be designed, constructed, equipped, and operated to forgive the errant user and protect the innocent victim."
"When serious hazards are foreseen or encountered on a project, positive protection should be specified and an associated pay item provided..."
In 2021, California launched its award-winning Caltrans Positive Protection Program which directs Caltrans design engineers and contractors to use Positive Protection to ensure worker safety. California research found a cost benefit for highly mobile barrier of $1.9 million per year, per barrier in 2008 ($2.87 million in 2025 dollars). [19]
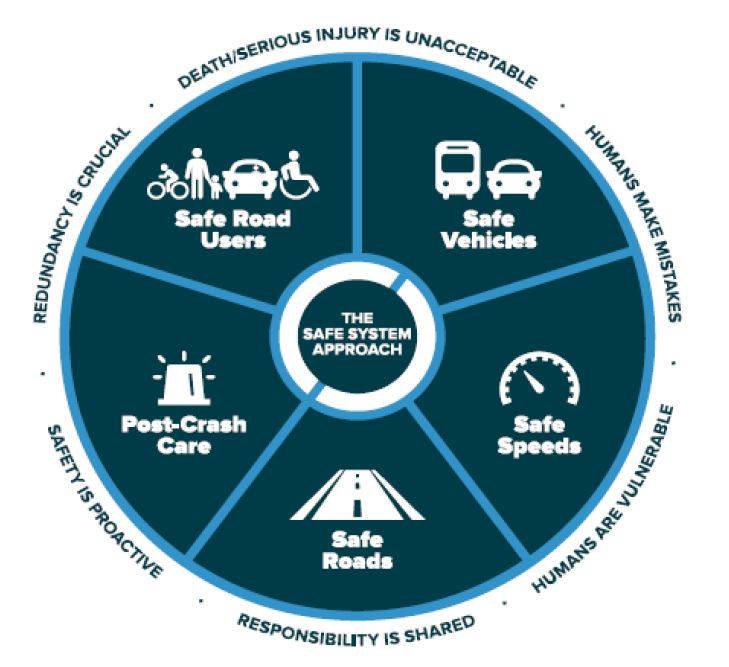
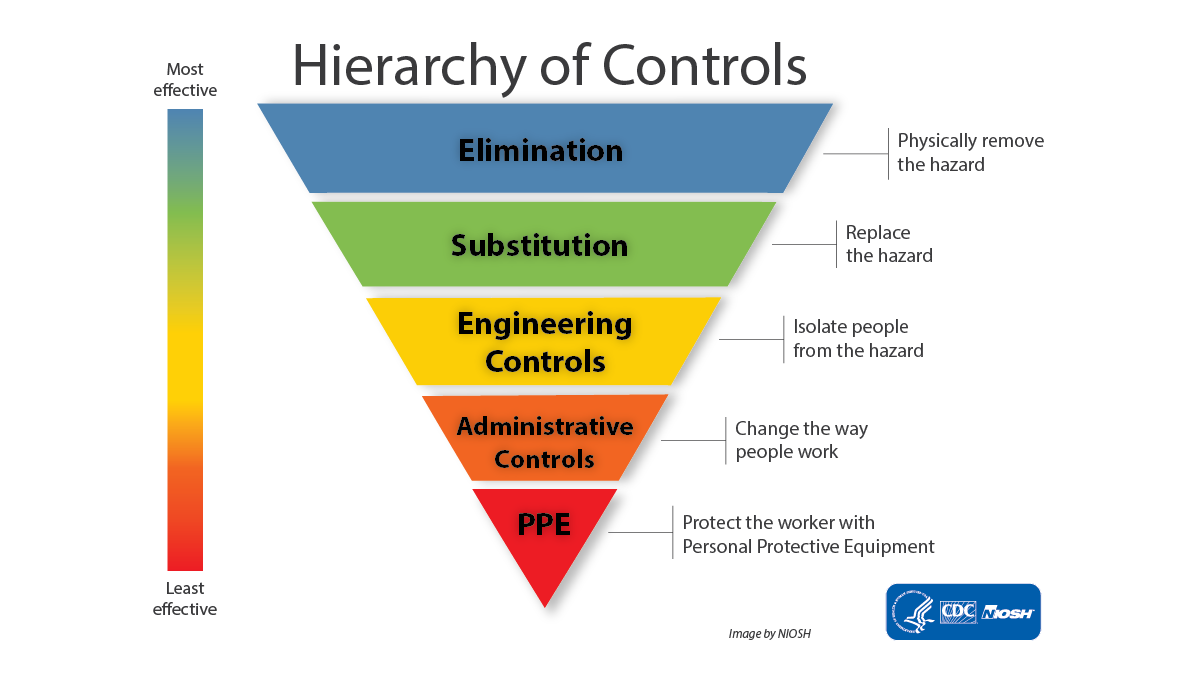
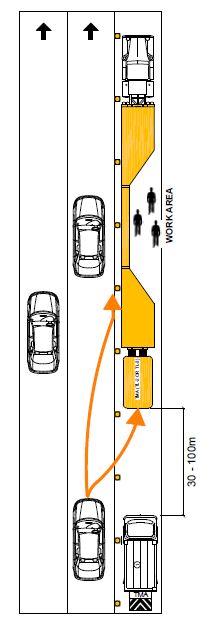
“A physical barrier provides one of the best possible protection solutions for workers exposed to the flow of traffic. [Implementing Positive Protection] is a common-sense and cost-effective way for safety reform that will prevent death and injuries of workers on roads and highways.”
Why is it so Important to Speak up about Work Zone Safety Issues?
"There’s no ‘pretty close’ when it comes to safety on the job. Almost safe means something needs to be corrected immediately before someone gets hurt or killed."
Improved worker safety is a proven benefit from using Positive Protection work zone barriers. Speaking up about work zone safety issues could reduce risk & save a life.
"The project manager needs to constantly reinforce the message that safety will not be compromised for any reason, especially, cost or schedule reasons...A project that finishes on time and under budget should not be considered successful if a teammate is seriously injured...Projects having fewer safety problems usually have fewer quality problems."
A National Safety Council (NSC) survey found 58% of Americans working in construction feel that productivity or speed is prioritized over safety. [8] A recent Construction Dive article reveals that one of structural engineers' biggest concerns (who are responsible for scructures and bridges across the nation) includes overly aggressive construction project timelines (42% respondants).
"These issues represent safety hazards... The push to shorten project timelines can lead to compounding errors during construction... This push to go too fast and possibly cut corners can be combatted by a strong safety culture."
Compromising on safety can lead to severe injuries, fatalities, liability, and/or rework. [9] One example is a tragic and preventable 2011 incident which resulted in a serious injury resulting from engineers' choices to withhold Positive Protection. The incident and engineers' choices attracted statewide news coverage, numerous questions, concern for the safety of people constructing and maintaining the state's roads, and a $37.3 million settlement. This incident led to major safety reforms in 2019 through the enactment of a new law directing design engineers and contractors in the state to use Positive Protection to ensure worker safety.
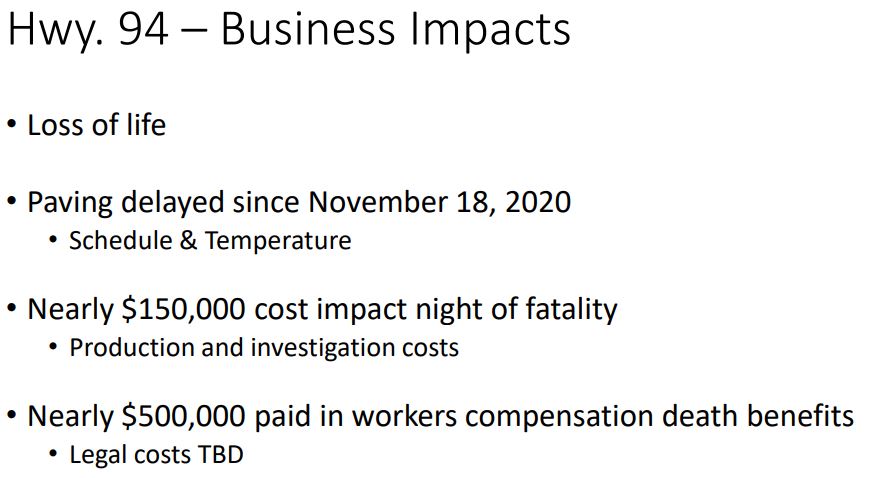
Work Zone Intrusion Example (April 2021 CPWR webinar).
In another example, in an April 2021 CPWR webinar, a highway contractor reflected on business impacts from a work zone intrusion on Highway 94 in California: Loss of life, project delayed more than 5 months since the fatality, immediate business impacts nearing $650k (~6.5% of contract value), and "legal costs TBD". In June 2021, the contractor joined in efforts at ARTBA calling on industry and roadway owners "to update state standard specifications to give stronger consideration to the use of barriers between workers and motorists." In September 2021, ARTBA issued its Policy Statement on Positive Protection.
Safety issues (i.e. the number of injuries) are strongly correlated with quality issues (i.e. non-conforming work or rework) on highway and infrastructure projects, according to recent studies. [13] Engineering News-Record (ENR) reports that "[A] growing body of research link[s] these sometimes separately considered dimensions of construction, avoiding rework and avoiding injuries. Often, haste in completing work is believed to spur workers and managers to take shortcuts that add to hazards...safety and quality overlap frequently."
On average, direct costs of rework on infrastructure projects amounts to over 5.7% of a project's total cost, according to some industry estimates. [10] [12] In addition, rework often adversely affects project schedules, leading to overruns and delays. [11] For large infrastructure projects, this can mean millions of dollars in unexpected expenses.
"An undeniable feature that contributed to both NCRs [non-conformances and rework] and safety incidents was human error [on infrastructure, rail, and building projects]; the fragility of human beings inexorably ensures that errors will occur...
In acknowledgment of this, ...there is therefore a need to ‘anticipate what might go wrong’ and accommodate the likelihood of errors occurring when undertaking a risk analysis prior to the commencement of construction...
When rework was required, for example, it was noted that people tended to take ‘short-cuts’...and there may no longer be equipment in place that supports a safe work environment...
People make mistakes, but organizations make it possible for them to be really serious."
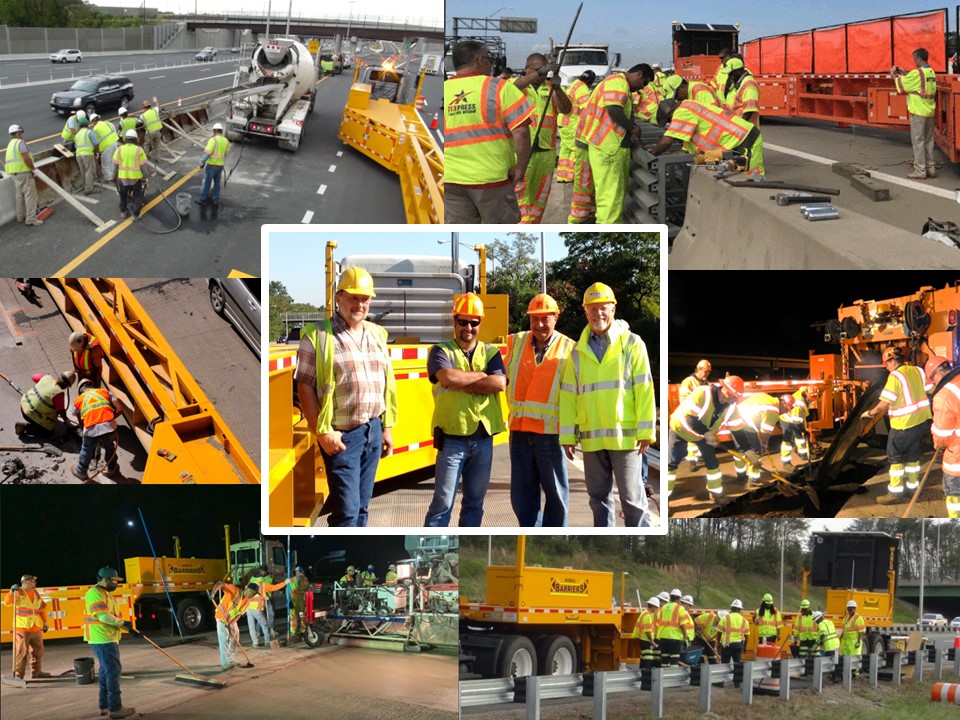
Comprehension Check - True or False? "Every day, highway workers put their lives in danger [from errant vehicles] just by going to work..."
False: The statement above is antiquated and no longer true. Today, we have the technology, 'know how', and responsiblity to protect workers from errant vehicles by using Positive Protection.
"Blaming human error alone is convenient, but it places all Americans in greater danger."
"Engineering has a direct and vital impact on the quality of life for all people. Accordingly, the services provided by engineers require honesty, impartiality, fairness, and equity, and must be dedicated to the protection of the public health, safety, and welfare."
"Members should hold paramount the health, safety, and welfare of the workplace and the public."
"Safety is a people profession. We want to help workers feel safe, contribute to organizational goals and return home healthy at the end of the workday."